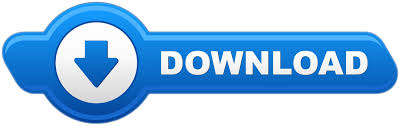


This is a short video I did at the weekend for someone who had only been using 2 and 2.5D and wanted some curves on some steel parts. Though you would usually do a roughing adaptive cut and then a finish or two selecting the best approach for each aspect of the part. For all of these you just select the overall shape or surface and the CAM will work out a single path, no need to string them together. When the tool really starts to move about is when you have compound curves such as fillets where one curved surface meets another and then you see all 3 axis moving all over the place at the same time. Also instead of the the tool doing a horizontal path each time it can be constantly ramping down in effect following a spiral around the shape of the part. The down side of this is if the shape is curved rather than just a straight angle then the horizontal stepover is less on near vertical surfaces and increases as they become flatter.ģD will follow the slopes and curves better and can adjust each "level" so that the step or scallop between cuts is constant no matter what part of a curve is being cut.
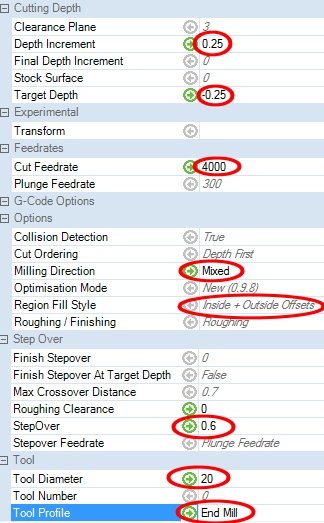
2.5D is when you increment down and run another horizontal and if that downwards increment means the tool needs to move sideways compared to the previous cut then that is how it copes with slopes doing them like contours on a map. I'd say 2D is horizontal and vertical surfaces only.
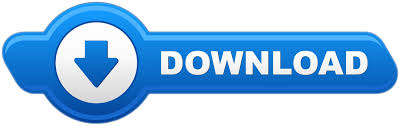